Optical Fibre based Artificial Compound Eyes for Ultrafast Static and Dynamic Perception
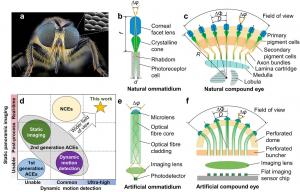
Concept and principle of the artificial compound eye for a panoramic camera (ACEcam) that uses conical-microlens optical fibres to mimic natural ommatidia.
GA, UNITED STATES, September 30, 2024 /EINPresswire.com/ -- Natural selection has driven arthropods to evolve compound eyes to achieve static and dynamic perceptions in complex environments. This inspired scientists from HK to develop a biomimetic artificial compound eye (ACE), which integrates 271 lensed polymer optical fibres into a dome-like structure, achieving real-time 180o panoramic imaging, depth estimation, and high-speed motion capture. These characteristics make this ACE suitable for applications to capture high-speed objects, such as surveillance, unmanned aerial/ground vehicles, and virtual reality.
Natural compound eyes (NCEs) were first investigated by Robert Hooke in 1664 after he observed orderly arranged pearls in the cornea of a grey drone fly. These NCEs then inspired the development of artificial compound eyes (ACEs) based on planar microlens arrays, curved microlens arrays, and metasurfaces. Nevertheless, none of those ACEs can match the NCEs in achieving real-time panoramic direct imaging and dynamic motion detection simultaneously. Specifically, the main challenge with curved microlens array-based ACEs is how to transmit the light rays collected by many microlenses on a curved surface to a flat imaging sensor (e.g., a CMOS chip) while maintaining their spatial relationships.
In a new paper (https://doi.org/10.1038/s41377-024-01580-5) published in Light Science & Applications, a team of scientists, led by Professor Xuming Zhang from Department of Applied Physics, Photonics Research Institute (PRI), & Research Institute for Advanced Manufacturing (RIAM), The Hong Kong Polytechnic University, Hong Kong 999077, China, and co-workers have developed a biomimetic ACE as a panoramic camera (called ACEcam hereafter). This ACEcam enjoys 180o field of view (FOV) versus 150–180o FOV for most arthropods, making it particularly well-suited for applications in areas such as surveillance. The real-time panoramic direct imaging without distortions eliminates the need for redundant post-processing methods, rendering the ACEcam more suitable for applications such as imaging and distance measurement among moving objects in real-world scenarios; a nearly infinite depth of field can enhance the sense of realism in augmented reality experiences, making it more niche in virtual reality and augmented reality compared to those lacking this property; translational and rotational motion perception capabilities and ultrafast angular motion detection (5.6×106 deg/s at maximum) provide the ACEcam with the potential for kinestate tracking and motion state control across various machines, from common cars to high-speed aeroplanes and even spacecraft. The amalgamation of these merits also positions the ACEcam for niche applications. For instance, the 180o field of view and ultrafast angular motion detection make ACEcam suitable for integration into obstacle avoidance systems for high-speed unmanned aerial vehicles. This capability reduces the need for multiple obstacle avoidance lenses, consequently eliminating excess weight and size. The 180o field of view and little size of ACEcam also let it suitable for endoscopy.
In the proposed ACEcam, lensed plastic optical fibres are used as artificial ommatidia. By adding a conical microlens to the distal end of the fibre, the plastic optical fibre mimics the function of an ommatidium, collecting and transmitting light to the sensing unit. A bundle of lensed plastic optical fibres evenly distributed on a hemispherical surface is assembled to mimic NCEs, and the proposed ACEcam demonstrates excellent static imaging and dynamic motion detection capabilities. These scientists summarise the operational principle of their camera:
“We design a microlens with a conical shape onto the distal end of the plastic optical fibre to decrease the light acceptance angle of a plastic optical fibre and thus increase the angular resolution. Our analysis and simulations show that a half-apex angle of 35o is the best choice for the conical microlens, reducing the acceptance angle of the fibre from 60o to 45o. Moreover, the sharp tip of the conical microlens is rounded during the fabrication process. This rounded tip is beneficial since it ensures that light information in the central angular range is not lost.”
“The conical microlens plastic optical fibres are fabricated in batches by a sequence of 3D printing, electroplating and two moulding processes, which is a novel approach to add a microlens onto the distal end of an optical fibre. Approximately 200 conical-microlens optical fibres are obtained in each batch process, and each conical microlens has a smooth surface and naturally a rounded tip.” they added.
“271 lensed plastic optical fibres are attached to a 3D-printed perforated dome so that all the lensed ends of the fibres are on the dome surface, while the bare ends of the fibres are placed into a perforated planar buncher. Light leaving the bare fibre ends is projected onto a flat imaging sensor via an imaging lens. The dome, the buncher, the imaging lens and a flat imaging sensor chip are hosted in a screwed hollow tube. In the assembly, the 3D-printed dome has the black colour so as to absorb the leaked or stray light, functioning the same as the pigment cells in the NCEs to prevent crosstalk. The lensed plastic fibres confine the collected light, preventing crosstalk and the associated ghost images, and the buncher maintains the relative positions of the microlenses on the dome. This setup enables the light collected at the curved surface to be transmitted to a flat image sensor, thus faithfully replicating the ommatidia in an NCE. In the image formation process, the light emitted by the object is captured at different angles by the microlenses on the dome. At the bare fibre ends, the planar images are projected onto the flat imaging sensor chip. Then, the final images are obtained for digital image processing. The imaging lens prevents contact of the bare fibre ends with the vulnerable image chip surface” they further explained.
“ACEcam holds the promise of becoming the cornerstone for future ACEs, owing to its synergy with diverse disciplines. For instance, the imaging optical fibre bundles can emulate natural ommatidia to replicate optical and neural superposition observed in NCEs, potentially enhancing ACEcam's imaging resolution and dynamic perception speed. Furthermore, the integration of optofluidic lenses with ACEcam presents an opportunity to harness the advantages of both arthropods' compound eyes and vertebrate monocular eyes.” the scientists forecast.
DOI
10.1038/s41377-024-01580-5
Original Source URL
https://doi.org/10.1038/s41377-024-01580-5
Funding information
This work was supported by the Research Grants Council (RGC) of Hong Kong (15215620, N_PolyU511/20), Innovation and Technology Commission (ITC) of Hong Kong (ITF-MHKJFS MHP/085/22), The Hong Kong Polytechnic University (1-CD4V, 1-YY5V, 1-CD6U, G-SB6C, 1-CD8U, 1-BBEN, 1-W28S and 1-CD9Q), and National Natural Science Foundation of China (62061160488, 52275529).
Lucy Wang
BioDesign Research
email us here
Legal Disclaimer:
EIN Presswire provides this news content "as is" without warranty of any kind. We do not accept any responsibility or liability for the accuracy, content, images, videos, licenses, completeness, legality, or reliability of the information contained in this article. If you have any complaints or copyright issues related to this article, kindly contact the author above.
