Automated additive manufacturing closes the gap between single-item and mass manufacturing
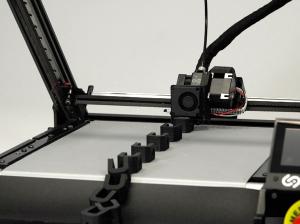
Serial production on the 3D belt printer One Pro - closing the gap between single piece and mass manufacturing
The device, which has been perfected for custom manufacturing, has been automated for real mass customization - By installing a conveyor belt as print surface
DüSSELDORF, NORDRHEIN-WESTFALEN, DEUTSCHLAND, March 22, 2023 /EINPresswire.com/ -- Mass production via injection molding or prototype production via 3D printer - are the common approaches in the industry. But for small batches or complex shapes in large format, there is still no general solution. Much is done using multiple devices, which often results in cumbersome manual steps or inefficient material consumption. One device that bridges the gap between traditional 3D printers and injection molding is the cThis exceptional machine promises additive mass production, and that includes extra-long models - printed hollow, with specific degrees of fill, or "floating" above the print bed with no support structures at all.Industrial mass production of individual parts is the job of machines that use injection molding. In contrast, 3D printers are primarily used to develop models, prototypes, or one-offs - the latter often for private use. However, there is a whole range of use cases whose requirement profiles fall somewhere between these types of production. Particularly in medical technology, the automotive industry, and aerospace technology, the demand for medium-scale complex products has increased in recent years. As a result, additive manufacturing is gaining use there. However, depending on the component, not all 3D printers are equally suitable. The quickest to fail is the respective build space; devices with correspondingly large capacities are a proper investment and not least, require even larger footprints. Only very few companies can afford this luxury. So if several components with notably different properties are required, different types of 3D printers are often more likely to be used. It is not uncommon for components to still have to be assembled manually. In turn, those who can't afford or don't want their own 3D printing farm to outsource production to external printers, which in turn counteracts fast turnarounds and reduced delivery distances that 3D printing is supposed to promote.
For anyone who lacks space and significant start-up capital but still wants to produce flexibly on-site as independently as possible, Düsseldorf-based iFactory3D GmbH has developed its One Pro 3D belt printer1. The device differs from conventional 3D printers in the following main features:
1. The printer can print cavities and overhanging shapes without support structures thanks to its innovative 45-degree angled print head. This results in lower material consumption during the printing process. Plus, direct time savings during the printing process and less time after the printing process. Since there is no need for post-processing of the printed objects by removing the superfluous printing structures, grinding, or melting.
2. Thanks to the conveyor belt as the length axis of the build space, theoretically infinitely long structures such as ribbons or tubes can be printed. With a corresponding mountable roller extension from the manufacturer, the print quality remains constant, as the center of gravity thus shifts later.
3. The belt enables serial production without supervision. This means that the press can run around the clock, over several days and weeks, as has already been demonstrated by a number of customers. In this way, high productivity can be achieved with a minimum of personnel, and the time spent printing in absentia literally passes as if in sleep.
The One Pro is more or less the result of an "emergency situation". It was triggered by unique parts that could not be produced with a conventional 3D printer yet were not needed in sufficient quantity to be built in any other way. In addition, the start-up capital for a corresponding external production order was simply not available. However, the project had to move forward, so Martin Huber (CTO and co-founder of iFactory3D), pragmatically developed a device that could meet all of his criteria. An all-in-one solution, so to speak. This system quickly convinced everyone who learned about it, and the actual tool overshadowed the original project, which it was only invented to fulfill. Martin Huber and his project partner Artur Steffen did not want to keep this "chance hit" to themselves and, without further ado, committed themselves to the publication of their all-rounder. With the One Pro, the vision the founders quickly had in mind of globally networked mini-factories to revolutionize production and logistics came to a step closer.
Another decisive factor in favor of the One Pro is the service. Thanks to an experienced R&D department2, iFactory3D offers German customers an extensive support service and individual consulting for project solutions related to 3D (belt) printing. The comparatively low acquisition costs of the printer are also convincing. In contrast to industrial AM machines, the One Pro is already in the black after a few weeks when it is well utilized. This makes it particularly interesting for start-ups or smaller companies, for example. Since the 3D belt printer does not set out to replace injection molding, the all-in-one solution for small batch production is also suitable for more established companies and all those who want to expand their range and become more agile. The content of elements produced is almost unlimited. From special fasteners to flagpoles, from household aids to art objects, from shoe heels to orthopedic insoles - anything is possible.
Another advantage of 3D serial printing is the sustainability aspect. CO2 is saved due to avoiding long transport routes, and a not inconsiderable amount of material is held in the production process. This is because, unlike injection molding or other methods that generate a lot of waste through milling and trimming, additive manufacturing, in which objects are built up layer by layer, is mainly loss-free. In the case of 3D printing, the most significant amounts of waste are generated by required support structures. And 3D conveyor belt printing can altogether dispense without the aid of these in a large number of cases by its design. True, 3D printing is not in a position to completely replace injection molding processes. But with innovative belt printers such as the One Pro, injection molding can be usefully supplemented, thus closing the gap between individual pieces and mass production3.
Artur Steffen
iFactory3D GmbH
+49 2111585657
email us here
Visit us on social media:
LinkedIn
Instagram
YouTube
TikTok
Facebook
Twitter
1 https://ifactory3d.com/en/one-pro-3d-printer/
2 https://ifactory3d.com/en/services/
3 https://ifactory3d.com/en/bachelor-thesis-confirms-economic-viability-and-applicability-of-3d-belt-printing/
