BIM BAM BOOM – The Firm Route to Enhance Design, Construction & Facility Operations
AEC stakeholders including architects, MEP engineering professionals and MEP contractors – all get benefited from BIM BAM & BOOM technique.
The rationale behind BIM BAM BOOM Technique:
The basis of BIM BAM BOOM is to inform Architectural, Engineering and Construction professionals on how to derive the maximum benefit out of a Building Information Model rather than using it as a design tool. An accurate information model avoids unexpected complications, risks and enhances the process of delivering a quality product. Through the BIM BAM BOOM technique of operation, a bridge is created amongst stakeholders involved in the project to maintain a consistent workflow and team orientated setting.
Regarding the functions of BIM, BAM & BOOM, Sukh Singh, V.P. Tejjy Inc. stated – “Building Information Models are playing a crucial role throughout the entire lifecycle of the building from the stage of conceptual design development, building assembly to facility management, maintenance & operation.”
Top 3 Stages of BIM, BAM & BOOM for AEC Professionals:
AEC stakeholders including architects, MEP engineering professionals, mechanical & plumbing contractors and electrical contractors – all get benefited from BIM BAM & BOOM techniques2 throughout the various stages of the construction project lifecycle.
• BIM for Design Development & Coordination: During the design-build stage, the building architects and MEP engineers share data amongst stakeholders using the IFC format for addressing conflicts during the pre-construction stage.
Key Benefits from the 1st Stage:
Collaboration: Construction professionals team up across time zones, without going onsite and getting access to the model any time. The Common Data Environment (CDE) in Building Information Modeling works like Google Drive for storing all data in one place. BIM engineers validate every design element before sending it to the building contractors.
Data Sharing: All information about the building energy consumption along with the position of every element including the wall, roof structure, etc. are shared with stakeholders before the project goes for tender.
Time & Cost Scheduling: Time, as well as cost scheduling, is applied to building parts in the design-build phase.
• BAM for Construction Phase Support from BAM: At the time of the construction phase, the building contractors, site managers, precast element suppliers and tradesmen derive the maximum advantages from BAM, providing data access from the 3D model. The technique integrates the entire work process of construction planning, material procurement and cost estimation.
Key Benefits from the 2nd Stage:
Reduced Miscommunication: BAM reduces miscommunication & creates a virtual model to be used by the construction site managers and the contractors.
Information Accuracy: The model enables team members to work accurately, providing significant information about different trades including piping, plumbing, steelwork, roof design, etc. and assess what the architects have designed at the initial phase of design development.
Decreased Clashes & Quality Management: Decreased conflicts facilitate improved quality management. BAM adds microchips to elements like prefabricated cement structure to ensure that it ends up at the precise location where the installation has to be made. The technology is effectively used in manufacturing for many years and is recently gaining popularity in construction.
• BOOM for Operational Phase: As soon as the construction gets over, the facility managers use the data elements of a 3D model and engineering for an integrated building operation and ongoing model management.
Key Benefits from the 3rd Stage:
Accurate Record of Building Facility: BOOM provides an accurate facility record, to be accessed throughout the building lifecycle anytime, anywhere.
Usage Management: Information retained in the facility encompasses space management elements, related to a department or occupancy tracking for optimized usage management. MEP drawings get easily integrated within building facility management and as a result of which maintenance, repair and energy consumption can be monitored successfully. The cost of labor could be easily tracked throughout the lifetime of the facility.
Managing Warranty & Maintenance: In the BOOM framework, bar-coding is applied throughout the construction and maintenance phases, facilitating monitoring of building items through asset management and tracking the lifecycle of various parts with the date of installation and physical attributes. Through BOOM implementation, the building system acts as a record keeper, warranty manager as well as a maintenance scheduler.
Process of Using BIM as BAM:
Using Building Information Modeling, construction professionals use the software application for digital model creation called BAM. The technique contains detailed project information with unique characteristics stored in a specific space, allowing easy access. Consequently, it becomes easier to create a building plan, make necessary modifications in the existing state, and maintain the facility asset after completion. Using the model, project managers determine the time and the cost, decreasing project risk. Moreover, BIM software helps to choose the right materials for the building environment.
Process of Using BIM as BOOM:
People have the delusion that Building Information Modeling technology is useful for the sake of designers and the construction team, but not for the clients. Nevertheless, this is not the case. This is because about 20% of the building cost resides in design and construction and the rest lies in effective facility operation. BOOM enables clients to analyze models from the feasibility stage and inspect them accurately, calculating the material cost at pre-construction.
Hold the Route of BIM-BAM-BOOM to Gain an Edge over Competitors:
BIM BAM BOOM is beneficial throughout the stages of design, build and operation, providing the ability to interrogate design models for validating engineering decisions. AEC industry professionals can show cost implications about design change, get rid of coordination challenges and provide safe operational methodology and logistics planning. Seek an integrated construction workflow with BIM-BAM-BOOM and optimize building design, avoiding clashes to aid building safety.
Do you want to connect construction schedules to BIM models? Contact BIM engineers of Tejjy Inc. at 202-465-4830 or info@tejjy.com and work in an integrated way for successful project completion.
sukhchain singh
Tejjy Inc.
+1 240-595-4210
email us here
Visit us on social media:
Facebook
Twitter
LinkedIn
Other
WATCH NOW: BIM Revolutionizing Construction Industry at https://www.youtube.com/watch?v=HqyUI-0Kt2o
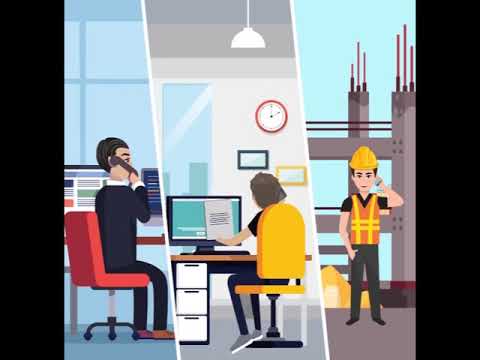
1 https://www.tejjy.com/our-services/bim-3d-model/
2 https://wiki.biminstitute.org.za/2016/09/16/09-bim-bam-boom-theory/
3 https://www.bimcommunity.com/technical/load/25498/navisworks-managing-bim-4d-simulation
